CALL OUR EDM TECH HOTLINE 800-346-9004

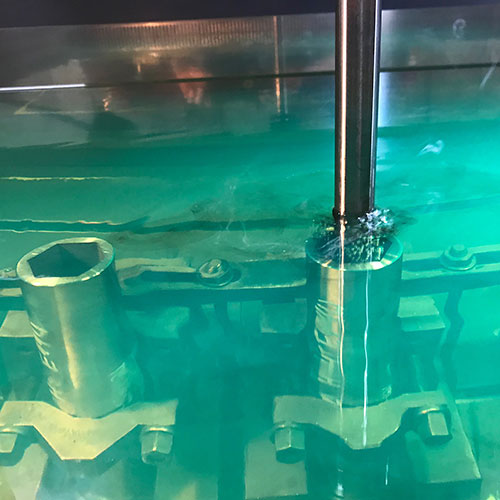
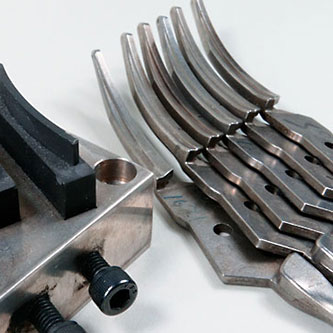

Sinker / Conventional EDM
Adron is experienced in the customer designed manufacture of tooling, prototypes, and precision parts for every industry.
Adron’s sinker department burns many exotic materials such as carbide, PCD and zirconium. We have 2 machines with Mitsubishi HPS power supply (high-speed tungsten carbide machining booster).
Although our sinker department is not nearly as large as our wire department, Adron is quite capable. With 7 CNC EDM’s incrementing in sizes from standard, toolroom machines for smaller parts, to our largest, a Mitsubishi EX 30.
With its X-Y-Z travels of 27.6” x 19.7” x 13.8”, and a maximum electrode weight of 330 lbs., this machine provides Adron enormous capability and we have processed many large parts, such as turbine rings.
Dick Quint, Adron’s Sinker EDM Manager reports that this 36” diameter, stainless steel ring, took a total of 160 hours to completely EDM. This required 43 graphite electrodes to produce 82 vanes and this part is presently part of Adron’s ongoing, long-run sinker production.
What is Sinker EDM?
Sinker EDM, also called cavity type EDM or RAM EDM consists of an electrode and work piece submerged in an insulating liquid such as, more typically, oil or, less frequently, other dielectric fluids. The electrode and work piece are connected to a suitable power supply. The power supply generates an electrical potential between the two parts. As the electrode approaches the work piece, dielectric breakdown occurs in the fluid, forming a plasma channel, and a small spark jumps.
These sparks usually strike one at a time because it is very unlikely that different locations in the inter-electrode space have the identical local electrical characteristics which would enable a spark to occur simultaneously in all such locations. These sparks happen in huge numbers at seemingly random locations between the electrode and the work piece. As the base metal is eroded, and the spark gap subsequently increases, the electrode is lowered automatically by the machine so that the process can continue uninterrupted. Several hundred thousand sparks occur per second, with the actual duty cycle carefully controlled by the setup parameters. These controlling cycles are sometimes known as “on time” and “off time”.
The on-time setting determines the length or duration of the spark. Hence, a longer on time produces a deeper cavity for that spark and all subsequent sparks for that cycle, creating a rougher finish on the work piece. The reverse is true for a shorter on time. Off time is the period that one spark is replaced by another. A longer off time, for example, allows the flushing of dielectric fluid through a nozzle to clean out the eroded debris, thereby avoiding a short circuit. These settings can be maintained in microseconds. The typical part geometry is a complex 3D shape, often with small or odd shaped angles. Vertical, orbital, vectoral, directional, helical, conical, rotational, spin and indexing machining cycles are also used.
Adron Tool Corp.
W251 N5490 Business Dr. • Sussex, WI 53089 • Ph: 262-255-4433
© 2022 Copyright Adron EDM Specialists. All rights reserved.